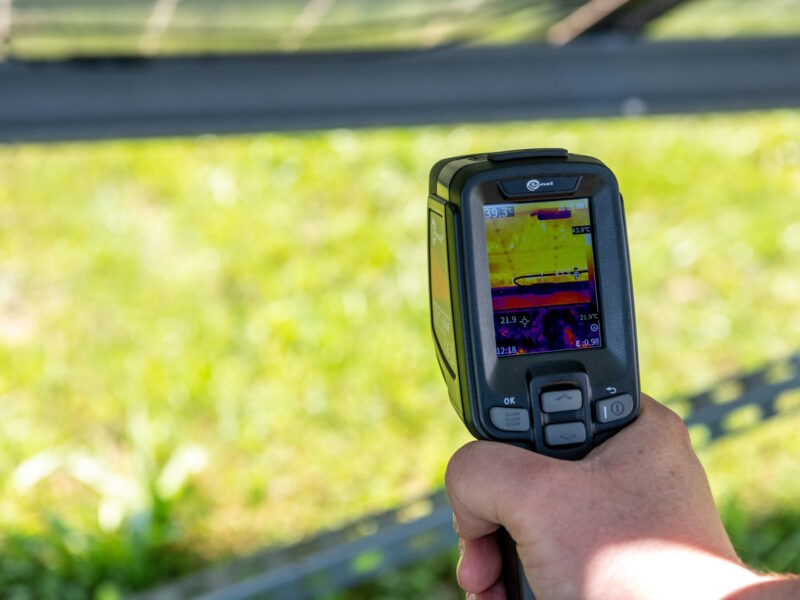
Inspections of photovoltaic installations with a thermal-vision camera Sonel KT-256F
The increasing popularity of photovoltaic installations makes investors more eager to set up such micro-installations on their land. Aiming to maximise the safety of such installations, the regular inspections must not only include the electric parameters, but also the heat parameters of the specific components.
Photovoltaic installations vs safety
Overheating components of photovoltaic installations pose a severe fire hazard. Their quick detection and identification is mandatory in terms of effective counteraction against such cases. In this situation, thermal-vision cameras become the perfect solution, as they offer the ability to perform a touch-free measurement of heat radiation of specific surfaces have the ability to provide assistance in discovering the exact spot or area which displays heating anomalies.
From the point of view of ensuring safety and counteracting failures, that matter is exceptionally important, as an increasingly larger group of users, installation and maintenance technicians specialising in such installations decide to add a thermal-vision camera to their toolset. It does not only allow to detect, but also to identify the overheating areas – regardless whether they are merely loose connections, a damaged panel, or inverter issues.
Selection of an appropriate thermal-vision camera for various installation sizes
Cameras with varying three-dimensional resolution coefficient are going to be required to match the dimensions of the dimension of the inspected installation – or, if viable – the use of an appropriate lens is going to be necessary. It is a complex issue, focused on the core question: what do we want to measure? With aim to maximise the precision of the measurement, it would be necessary to use a camera with the lowest possible IFOV parameter.
Why is that parameter of such importance? To ensure that we correctly understand and interpret the obtained results. When the dimensions of the inspected object are smaller than the calculated value, we must be aware that the value of infrared radiation per pixel is also going to be averaged for other objects surrounding our inspected component within the area of the specific pixel. For this reason, being aware of how we take a specific measure – the type of equipment we use and the measurement distance – is of great importance.
In addition, the lower IFOV value the better (of course, we must also be aware of the FOV value, as the classic method for โrepairingโ IFOV on paper is using a narrow viewing point of optics, which is not a mistake in itself, unless it reaches an extreme value). For this reason, the key aspect is the appropriate selection of the camera that matches our requirements in terms of its parameters, functionality, but primarily taking into consideration what it is that we want to measure and what effects we wish to observe.
Sonel KT-256F is ideal for inspecting small and medium-sized installations
The excellent IFOV coefficient is one of the features which distinguishes the new thermal-vision camera Sonel KT-256F. It allows to carry out inspections of photovoltaic installations even from a distance of 17.5 m – in accordance with the guidelines laid down in IEC TS 62446-3, which sets out requirements for thermal-vision cameras in the scope of inspecting PV installations.
The handy Sonel KT-256F camera (or its cheaper alternative without autofocus function, i.e. Sonel KT-256) is an ideal tool for inspections related to the maintenance of small and medium-sized installations. These cameras are a tailored proposition for installation and maintenance technicians of photovoltaic installations (as well as heat pumps and other HVAC installations, as well as for civil engineering constructors and electricians). Due to the ability of running for 16 hours straight on a single battery charge, we can be sure that the camera is going to run for the entire day of taking measurements without the need to carry spare battery sets; if a need arises, the camera can be charged even with a power bank through its USB-C port.
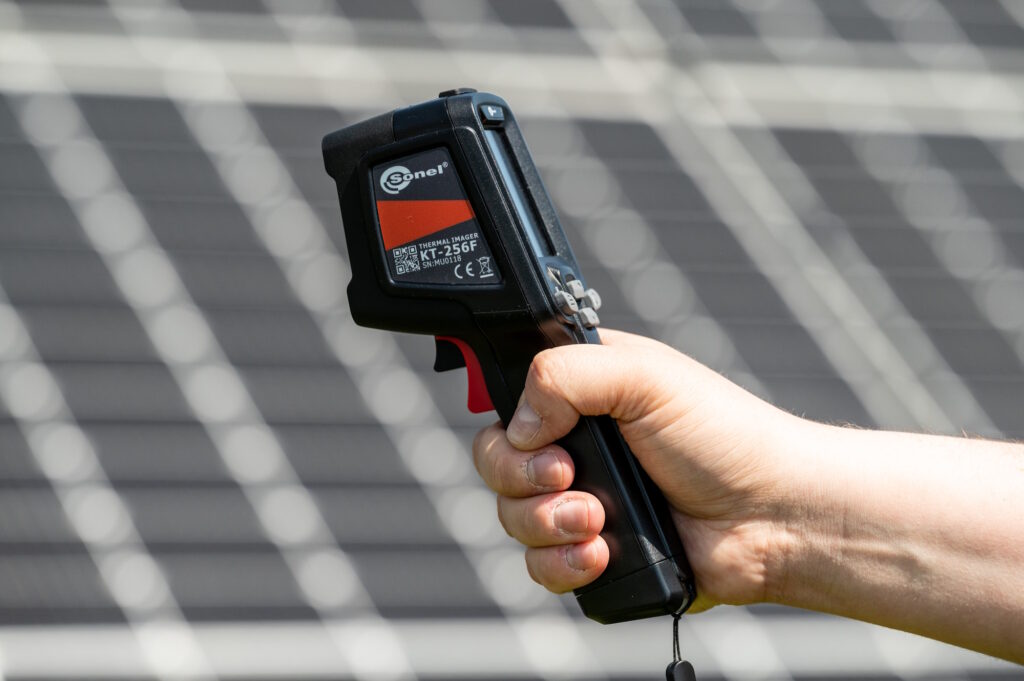
Photo 1. Inspecting PV installation with the thermographic camera Sonel KT-256F
The key aspects of thermographic inspection of photovoltaic installations
The first of the considered components is the photovoltaic panel itself. In case when one or more cells are in shade, while the remaining ones remain completely lit by the Sun, the heat gets stored on the cells in shade. It is a loss, poses a risk of a fire and a risk of damaging the photovoltaic panel. Overshadowing causes the reversal of polarity, which, in turn, causes the increase in electric resistance in the cell, and – in accordance with the laws of physics – voltage decrease generates heat. Thermal-vision camera allows to identify the cells with that issues, and to identify and localise the damages.
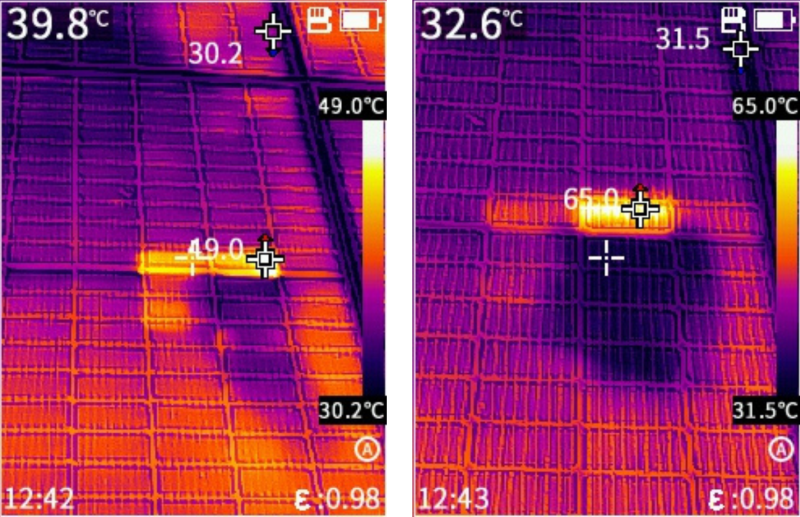
Photo 2. A thermogram of a damaged photovoltaic panel
The second aspect is the condition of the MC4 or Amphenol connections. Unprofessionally made connections may cause overheating. This generates a severe fire hazard. Please remember and pay particular attention to the fact that the connection carries direct current, and the DC arc does not extinguish as easily as an AC arc (generated when carrying alternating current). That phenomenon is caused by the fact that contrary to alternating current, the value of direct current does not cross the โ0โ threshold, as in the case of reversing polarity in the AC current, so it does not extinguish by itself. From the perspective of fire safety, that phenomenon is exceptionally dangerous and generates a significant risk of causing ignition of the installation and the construction on which it rests (ceilings are particularly vulnerable to ignition).
The third aspect is the possibility of verifying the improperly working inverter components. It allows to uncover irregularities in the connections (overloaded connector or other failures). Improperly tightened electric connection may generate a significantly larger fire hazard. Loosening the contact on the connector causes the resistance to increase, which causes the generation of heat on the connection, which can be discovered using an IR camera.
Author: Marcin Magierowski, Sonel S.A.
Products mentioned in the article:


No Comment